In the offset printing process, the printed matter is a common quality problem, which causes the printing ink to be smashed, leaving a graphic imprint similar to snowflake dots; the heavy ones cause the printing products to stick to each other, and the separation is difficult. Seriously affect the quality of printed products, and even cause the printed products to be scrapped. This will not only cause serious economic losses to the company, but also affect the reputation of the company, which should attract everyone's attention. Based on my long-term work experience in offset printing, the author has summarized seven common prints that are easy to stick, and analyzed the sticking mechanism one by one, and proposed a coping strategy for colleagues to learn from.
Seven common prints are easy to stick
1. Gold and silver ink printing
Gold and silver inks are formulated from special binders and gold and silver powders, and the penetration on paper is much smaller than ordinary inks. When printing characters and patterns using gold and silver inks, the oxidized and conjunctiva on the surface of the paper is slow, and the drying time required is long, which tends to cause the printed matter to be dirty.
2. Field printing
In order to print the solid effect on the paper, it is necessary to increase the amount of ink, but when the paper is saturated with ink, the excess ink will accumulate on the surface of the paper, so that the oxidized and conjunctival speed of the ink on the surface of the paper becomes slower, and the required drying time becomes longer. Long, which makes it easy to make the prints dirty.
In addition, when printing character hair or printing characters by four-color overprinting, since the total amount of ink per unit area is saturated, the ink layer is thick, which is particularly likely to cause the printed matter to be dirty. According to statistics, in the case that all printed products are dirty, printing a character's hair and using four-color overprinting to print the text causes a large proportion of the printed matter, which cannot be underestimated.
3. Special paper printing
Special paper refers to paper other than conventional coated paper, offset paper, white paper, etc., such as the brands of Gretel, Glas, Pure Wood, and Meisha used by the author's company. Due to the special papermaking process, the special paper makes the printing effect unique, which is favored by some users, so it is more and more applied to the printing of the cover and the inner page. However, the porosity of the surface of the special paper fiber is low, and the adsorption of the capillary to the ink is weak, which causes the ink to not easily penetrate into the inside of the paper, which easily causes the printed matter to be dirty.
4. Improper printing pressure
In order for the ink to transfer well to the paper, the printing pressure must be appropriate. The relationship between printing pressure and ink transfer amount is shown in Fig. 1.
As can be seen from Fig. 1, the AB segment indicated by the broken line is the irregular phase of the printing pressure and the amount of ink transfer; the BC segment is the phase in which the ink transfer amount increases as the printing pressure increases; the CD segment is printed. The feasibility phase of pressure and ink transfer is relatively constant; the DE segment is the stage where the printing pressure begins to be too large and the ink transfer amount begins to be unbalanced; the EF segment is the stage where the printing pressure is too large and the ink transfer amount is seriously unbalanced. Among them, P3 is the ideal printing pressure point, and P4 is the critical point of printing pressure.
As can be seen from the above analysis, the amount of ink transfer varies with the printing pressure. In actual printing, if the printing pressure is too large or too small, the ink can not be transferred well, and the dot can not be perfectly restored, making the color chasing difficult. In order to achieve the proof effect, the operator usually increases the amount of ink, which will cause the print to become dirty.
5. Too many paper stacks or misfeeds
In the actual production process, sometimes for the convenience of the map, the task is often used, the operator often replaces the paper table after the paper is full of paper, which creates a hidden danger for the printed matter. The ink is transferred to the paper and is not sufficiently dried. If the paper is stacked too high, the paper on the bottom layer will be subjected to a large load, causing the print to stick. In addition, if the delivery mechanism is improperly adjusted, the paper may be misaligned or misplaced, and the paper may be dirty on all four sides.
6. Dusting pipe is blocked
Installing a dusting device on a four-color offset press (less infrared drying) is an important means of preventing the print from sticking. However, this sometimes happens: the digital display of the dusting device indicates that the amount of powder is large enough, and the amount of powder in the container is sufficient, and the printed product is still dirty. After investigation, it was found that the powder spraying pipe was blocked by impurities, which caused the powder to flow unsmoothly, which caused the printed matter to be dirty.
7. Ink emulsification
After the ink is emulsified, the "oil-in-water" form is formed, which changes the performance of the ink. When printing with the emulsified ink, it is easy to cause the printed matter to be dirty. Even if the paperboard is clamped and the amount of powder is increased, it is not necessary. Replace the ink.
preventive solution
1. The pressure is slightly larger, the ink layer is slightly thinner
In actual production, the control of printing pressure is a very important part. As can be seen from Figure 1, it is necessary to control the printing pressure to about P3 (this is only a principle, the specific thick paper, the printing pressure value, but also the experience of the captain), can also control the printing pressure Slightly higher than P3, so as long as the preset ink amount reaches the graphic requirements, even if the ink volume is slightly lower, the ink is very full, the thickness of the ink layer is basically within the tolerance of the paper, the oxidized film is fast, and the printed finished product or semi-finished product is finished. No dirt will be produced. In order to increase the operability of the printing process, the author provides the following experience: strictly control the amount of ink when the printing pressure meets the standard, and often press the ink with the finger as usual, if there is anti-stick feeling and there is no excessive ink on the finger The printed parts thus printed will be unmistakable and will not easily cause the printed matter to be dirty.
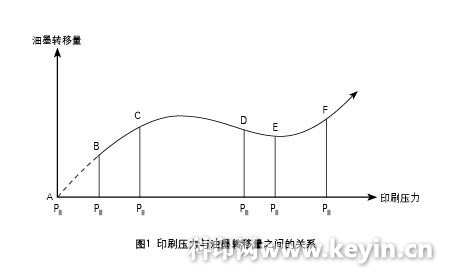
Airline Container Series
Smoothwall Microwave Aluminum Foil Trays Airline Food Packing Foil container
Description - Smoothwall microwave aluminum foil trays
1 - Smoothwall aluminum tray is a new and perspective type of disposable food package in the world .
2 - This type of trays is made of special alloys, which gives them a special strength. The sides of the tray have a completely flat and smooth surface, that`s why they can be hermetically sealed with foil or a plate made of foil.
3 - The resulting tray for sealing is made of smoothwall aluminum tray (smoothwall) will be not only strong and tight, but also environmentally safe. By the projections of analysts, smooth-walled metal trays for sealing will become a strong competitor in plastic trays for sealing with the film in the next 5 years due to the arrival of Western fashion for ecological compatibility.
Technical Parameter - Smoothwall microwave aluminum foil trays
Item No. | Specification | Item No. | Specification | ||
EM-202 | Top out | 168×108mm | EM-207 | Top out | 171×103mm |
Base | 149×88mm | Base | 134×69mm | ||
Height | 35mm | Height | 34mm | ||
Capacity | 380ml | Capacity | 340ml | ||
Packing | 1000pcs/ctn | Packing | 1000pcs/ctn | ||
Item No. | Specification | Item No. | Specification | ||
EM-212 | Top out | 121×108mm | EM-216 | Top out | 135×103mm |
Base | 77×65mm | Base | 103×73mm | ||
Height | 32mm | Height | 34mm | ||
Capacity | 220ml | Capacity | 280ml | ||
Packing | 1000pcs/ctn | Packing | 1000pcs/ctn |
Application -- Smoothwall microwave aluminum foil trays
Airline Container Series,Airline Container,Airplane Containers,Aircraft Shipping Containers
Zhengzhou Eming Aluminium Industry Co., Ltd. , https://www.emingalufoil.com