(BINGING AND FINISHING) Sew binding refers to a binding method that staples together a book with a needle, thread, or rope. This method is mostly used to bind strong, durable books such as encyclopedias, reference books, art books, and the Bible. For more than a hundred years, the most commonly used stitch binding method is the “Smyth†binding method, which is a binding method that passes a binding line through the spine and puts the pages together. The advantage of using this method is that after the pages of the signature are bound together, they can also be spread flat. Sewing binding is available in both side and saddle stitching forms. Bookbinding is the passing of a gutter through a book in a direction parallel to the spine. Like some publications, the sideline method is often used, and the side binding method is securely bound, but it cannot be completely unfolded. Handbooking is most commonly used when working in a library or doing book repairs; when using machine side stitching, the needle is attached with a thread through a drilled hole, and the pages are joined together in the form of a square thread. The two-wire binding adopts a structure similar to a household sewing machine needle and a bobbin. The difference from the sewing machine is that the needle passes through the drilled hole of the sewing thread and joins the pages together. Saddle stitching is the method by which the binding passes through the signature along the middle fold and binds the pages together. Because saddle-stitched books are easy to spread out, this type of binding is more common than side-stitching. In automatic saddle stitching, signatures are transferred from the hopper to the feed saddle where a scanner is installed to monitor the entire operation. A roller presses the signature on the protective screen in front of the feeding saddle, and the conveyor belt transfers this signature to the saddle for binding. After stapling, a separator separates the gutters and the books fall on another conveyor, which is shipped to the trimmer and delivered or shipped to the assembly line. Trimming machine Trimming machine is the device that cuts out the folded or uneven parts of the book block to form a neat and smooth edge and can cut all the adhering pages. In addition to mechanical binding and loose-leaf binding, it follows the entire nailing process as part of book finishing or online bookbinding. The edge trimming machine consists of a knife, a book and a file, and a back file. This system can cut the top, bottom and side of the book at the same time without changing the settings. Most of the book blocks are completed by trimming the three-knife/five-knife trimmings linked to the saddle-stitching machine and perfect binding in the finishing line. The edge trimmer cuts out excess parts of books or magazines from the top, bottom and edges. As part of the entire bookbinding flow line, the book block is automatically transported from the binding machine to the trimming machine, while the trimming machine may be cutting another book block while trimming the front edge of a book block. Back edge. Each book block is loaded on the feed guide of the edge trimmer and sent to the side knife where it cuts both the top and the bottom of the book block. When the side cutter is removed, the front cutter trims the edge of the book block and removes the overlapping pages of the folded book so that each page can be opened. The transfer jig lifts up the cut book block and places it on the conveyor belt, after which the book block is sent to a register or stacker. The air blower blows away the confetti on the trimmer so that the machine can trim the next book block. If a book block is printed in double-spread, that is, two sets of books are printed and bound together, then before cutting on three sides (if not too thick, it may be a five-sided cut), the entire book must be sawed open. The five-sided trimming machine can also handle three-print book blocks. Bookcase staples Bookcase binding refers to the process of adding a layer of cloth or leather outside a hard or soft cardboard to form a bookcase that is bound together with the book block into a hardcover book. The book cover, ie the book cover, is not prepared together with the bookbinding or binding. When adding a book shell to a book, the book shell area is larger than the area of ​​the book block page. When the book cover is prepared for the book cover, it is usually performed after the book binding is completed. Before entering the bookcase, the cardboard is first stuffed into a machine and cut to the right size. When making the book shell, the book making machine sticks the cardboard and the backing material together, rotates the excess cover cloth under the cardboard, and applies glue on the inside of the cardboard, and bonds with the cover cloth to form a smooth hard shell. At this time, the bookcase without the preprinted pattern may also be subjected to embossing and the like, and then the bookcase may be adhered to the book block. The next series of work is how to combine sewing or binding books with bookcase binding to form a hardcover book. In fact, this is part of bookcase binding. Spine flattening and signature squeezing: Squeeze binding books need to be flattened to remove excess air between pages and reduce book bloat during binding. Spine flattening exerts pressure on the spine, while flattening the signature stresses the entire surface of the book before and after. Harder paper generally uses a booklet flattening method because the spine is flattened and softer. The drive chain feeds the spine of the book block down into the spine flattening device. Here, a spring clamp clamps both sides of the book to prevent the book block from falling out. Afterwards, the signature presser began to press the entire book surface evenly to perform the flattening work. The applicator pressure is approximately 250 tons. Round and Rise: These two processes are used in both perfect binding and binding books. Rounding is the first process used to make the book block into a specific shape and then used for the upper cover. It forms a convex circle on the back of the book block and a concave shape on the edge of the book. This part of the work is accomplished by moving the book back and placing it between two relatively rotating steel drums. Side-bound books cannot be rounded. Rising the spine is to complete the rounding process and sandwich the book edge to project the back of the book from the middle to both sides of the book, forming two ridges on the back round edge. It can make books more flexible and durable, and strengthen the connection between the signatures. It also makes the width of the back of the book larger, provides a shoulder lift for the book shell behind the book block, and makes the binding between the book block and the book shell more robust. Backing, trimming and top strap are three other follow-up procedures. Backing can help keep the back of the book, while trimming and top tape are the means of decoration. After the above process, the book can enter the bookcase binding line. Sticky Book Shell and Spine Pressure Drying: The upper shell process consists of two steps: sticky shell and spine press drying. The sticky book shell is the sticking of the cloth cover to the book block. The front and back of the book block and the inside of the book case are coated with adhesive on all four sides, and then the cover is glued onto the book block. When sticking, make sure that the edge of the cover is evenly and evenly beyond the edge of the book block. The oversize is the same, and then it is pressed tightly. Spine compression drying refers to drying the binder of the adhesive shell under pressure. A series of pressure plates and thermoformed plates hold the book glued to the book case to make it stick. These pressure plates and thermal plates will hold the books under a lot of pressure and allow them to dry for a while before they are released. A book may need to go through five or more pressure plates and thermoforming plates depending on the degree of drying. The efficient bookcase opportunity combines all the processes, including rounding, ridges, sticky shells, oven drying, and bookcases, to form a mechanized production line. Bookcase binding. Bookcase binding can be divided into three categories: large hardcover, small hardcover, and library decoration. This classification is based on the quantity and nature of the binding. Most hardcover book books fall into the category of big hardcover. Large hardcover refers to a larger number of hardcover binding methods. Because this type of binding uses more automatic or semi-automatic binding equipment, its number of operations is generally not less than 1,500. Small hardcover is a small amount of hardcover binding. It is mainly used for manual operations and also for books that cannot be machine-bound, such as the Bible wrapped in soft leather. Library decoration is a special binding method commonly used in libraries. It includes pre-binding, renewals, and general repair work. The library binding machine is similar to a small hardcover machine and can be used to handle a smaller number of binding jobs, requiring more manual operations. The main purpose of this binding is to increase the degree of wear resistance of books commonly used in public libraries. Book Finishing Online Finishing Online finishing can be used as part of a web-printing process to replace some post-printing processes and do some work on printed products. It includes labeling, folding, die-cutting and other processes. Cover pressure embossing and embossing and other work can be completed in the online finishing, but also as an independent processing process. Offset presses for printed publications and books often use a compound folding machine to cut and fold the paper into signatures for later binding work. Other special accessory devices, such as pre-folders and plow-folders, can also be connected to on-line processing equipment to increase work efficiency. Online finishing differs from the post-press independent finishing, which combines several processes of post-press processing. Special craft sales point posters, stationery, menus and greeting cards all require special finishing techniques. This article will discuss finishing techniques related to pressure relief, foil stamping, and die cutting. These processes can be included in the post-press processing system, the online finishing system, etc., or they can be used alone. Pressure relief. Pressure relief is to use the mold to press out the raised graphics. This method is also used to suppress dark lines, but it does not use aluminum foil, ink, etc. to decorate the graphics. Indentation is the use of a mold to emboss a graphic on paper. The embossing machine consists of an embossing bed, a temperature-controlled embossing plate and a convex stamping die mounted on it. On the opposite embossing plate, there is also another mold corresponding to the stamping die and installed therein. The stamped printing material is also loaded in this platen. In press embossing, when the platen comes into contact with the press and begins to pressurize the printing material, imprints are created. In the embossing process, cold molds can be used for indentation, but hot molds are more common. Pressed gold foil. Pressed gold foil refers to the entire process of stamping the gold foil passed through the printed substrate of the heated mold and the feed roller with a press. When the machine is pressurized, the gold foil is pressed against the printing substrate. If flat pressure is used, the gold foil on the substrate will not be indented. The gold foil embossed pattern combines the above-mentioned pressure relief process with a pressed gold foil process. Book covers, cosmetic packaging boxes, and greeting cards are three products that are often pressed with gold foil and gold foil embossing. Die-cutting. Embossing and embossing are often performed immediately before or after the die-cutting process. If the corresponding attachment equipment is installed on the die-cutting machine, embossing and embossing of gold foil may also become part of the die-cutting process. Products that require die cutting include labels, paper boxes, popular books, point-of-sale posters, and more. Steel rule die cutting is a common die cutting process. It integrates die cutting, creasing and embossing, and can automatically die-cut one by one or in groups (two or more in each group). Die-cutting machine with pressure plate and roller type two. The platen die cutter works the same as the embossing machine described above. One platen carries die-cutting and embossing dies, and the other embossing plate carries matching dies. When the two plates are pressed together, die-cutting and embossing are completed. In a reciprocating platen die cutter, the position of one platen is fixed and the other can be moved toward it. Claw Platen Die Cutting Machines Both platens can move. When the two plates meet, die cutting and embossing begin. The platen die-cutting machine can complete 9000 impressions per hour.
Wax tealight candle
Material:Paraffin wax ,Soy Wax, Coconut Wax
Weight:8g to 23g
Package:50pcs/bag,100pcs/bag
Burning time:0.5hrs-8hrs
Color:white, red, blue, yellow, green etc
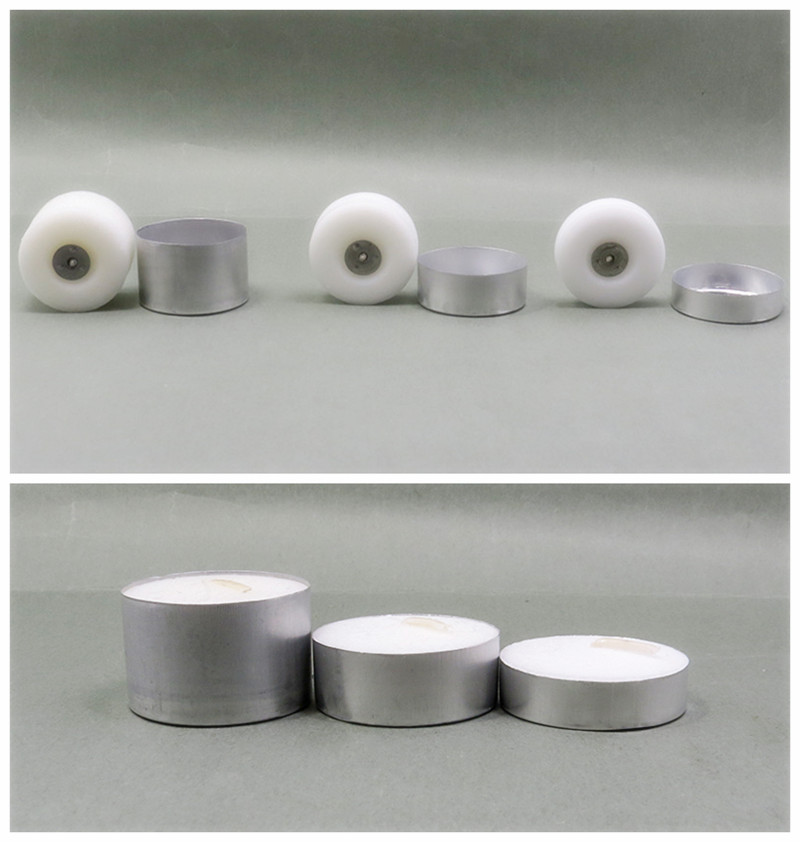
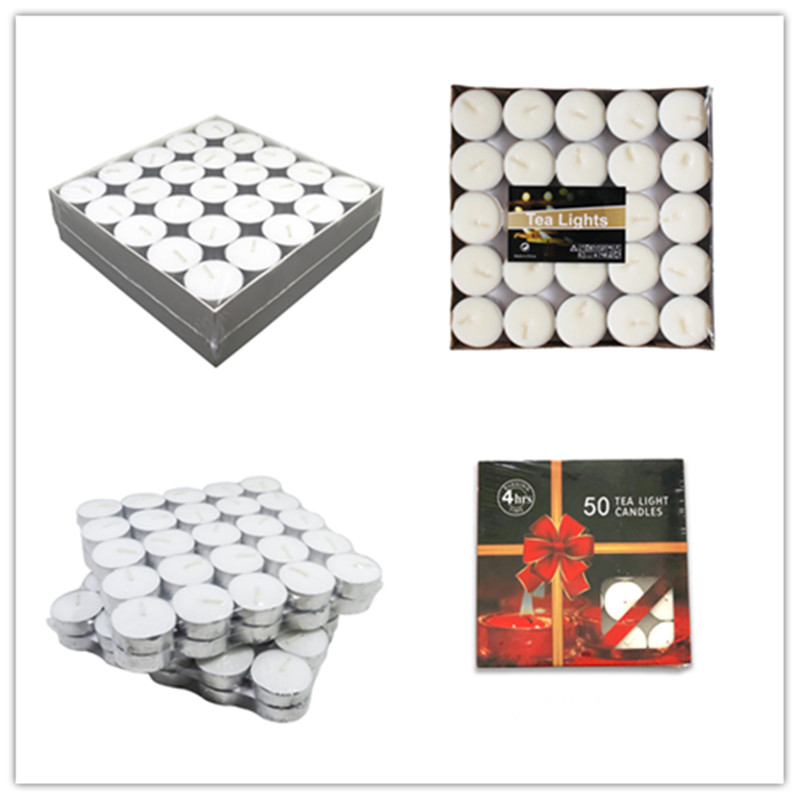
Tealight candle,Tea light candle,Wax tealight candle,Paraffin wax tealight,cheap price white tealight candle
China Senbo Industry Co.,ltd , https://www.yylpaper.com