Screen printers have come up with a rule that when the dots exceed the range you can print, a "pinhole" phenomenon occurs. There are two views on the “pinhole†phenomenon among printers. The first view is that the “pinhole†phenomenon is an irritating but inevitable thing in the process of screen printing; the second view is : All "pinholes" are completely preventable. This is a minority and radical view. I belong to the minority who agree with the second viewpoint. This article analyzes how to make a screen without a "pinhole". What is said here is not occasionally getting no "pinhole" screen, but consistently obtaining no "pinhole" screen. I know I can do this because in our screen printing lab, I have created a "pinhole" screen for six consecutive months. But before you talk about the production process, you must first understand three things about the "pinhole": 1. "Pinhole" is no longer happening for a reason; 2. Know what causes the "pinhole" phenomenon; 3. Each of these factors can be changed and avoided. Let's examine the entire screen production process, what caused the "pinhole" and identify the preventive measures. The original screen making process and the “pinhole†prevention step start from the original production workshop. The original production workshop is the place where the original image is obtained and the positive film (the positive film used to make the screen) is obtained. The original image and positive image film should be clean, scratch-free, and have no dark spots. The image area should be completely opaque or nearly opaque with sharp edges. If you use an original image with any of the following conditions, the likelihood of “pinhole†will increase: 1. Black spots appearing in emulsion or laser printing powder; 2. There are dirty spots or dust; 3. There is residual tape; 4. Multi-layer film or sulfate paper stick together; 5. Sulfuric acid paper original image. The main cause of "pinholes" is dirty original film. If you carefully clean the film, you can reduce the probability of "pinholes." The film original image can be cleaned with any kind of film cleaner (available through the screen printing supplier) and is preferably cleaned with a designated cleaner because other cleaners may scratch the film, cause static build-up, Or the detergent left to absorb dust. The acquisition of screens without "pinhole" screens also requires very clean screens. The wire mesh must be chemically cleaned, and it should be cleaner than the clothes you wash in the laundry and the plates used on the dinner table. To obtain a clean screen, you must have a pressure washer that sprays at 1000 psi. You must systematically and thoroughly clean it with specific industrial cleaners and detergents (never use household cleaning. product). After the screen is cleaned, remove it from the tank; rinse the tank, place the screen back into the tank, and rinse the screen for more than three minutes. Never put it in a dirty cleaning tank. In the large-scale screen production workshop, you can prepare two cleaning tanks: one dirty cleaning tank for stripping the screen, one clean cleaning tank for final screen cleaning and imaging screen development. In addition, the screens are dried in an environment that is dust-free (especially not on the floor) and without air flow (in front of the fan) because the air flow can cause dust. A common source of neglected dust “pinholes†is dirty water from a film or mesh frame to the image area of ​​the screen. Therefore, the frame must be level when drying the screen. There is one thing to note when requesting a clean screen: Corrosion-inhibiting removers can be dirty, but if they are used for too long or too many times, the elasticity of the screen may be reduced. It is safer to use a non-corrosive, fuzzy remover, and also to discriminate between the dust that must be removed from the screen and the spots on the screen that do not cause “pinholesâ€. Immersion emulsions that are not well-mixed with the emulsion may also be a source of "pinholes." If you use a diazo sensitizer direct emulsion, you must ensure that it is completely dissolved in water before adding the diazo powder to the emulsion. Undissolved small particle diazo powder will cause "pinholes." When you dissolve the diazo powder, check the white liner on the container mouth of the heavy nitrogen sensitizer. If there is a brown spot, it means there is no complete dissolution. After mixing the diazo sensitizer with the emulsion, store it for at least one hour to allow the bubbles to drain completely. Another source of "pinholes" is dust in the emulsion. When pouring unused emulsions back into the emulsion tank, be aware that if any dust, cloth, small obstructions, or other contaminants enter the emulsion, it may result in a “pinhole†when the screen is next produced. The advantage of a matt film is that it is less likely to create "pinholes", and the recently developed dual-cure direct emulsions are also less likely to produce "pinholes" than previous methods. If you are using a direct emulsion, It is recommended that you test with a new product. The next aspect of exposure equipment to prevent "pinholes" is exposure equipment. No pinhole screens can be made with any commercial screen exposure equipment on the market, but there are some devices that have a high probability of producing "pinholes." The light source is a key factor in the screen exposure unit. A metal halide lamp with an effective output of 1-5 kilowatts is considered to be the best light source. It has the rich wavelength light and low heat output needed to expose the image stencil emulsion. Followed by mercury lamps. No matter what light source you are using, your exposure unit should have an optical integrator. Since the lamp that exposes the screen can not always emit the same amount of light, if you measure with the timer, the lamp that may be correctly exposed on Monday will be underexposed on Tuesday. The two most common causes of changes in the output energy of the exposure light source are lamp life and unstable current. The light integrator controls the actual amount of light received by the coated screen by monitoring the actual amount of light emitted by the lamp. This is the most accurate measurement method that can improve the reliability and consistency of screen exposures, and avoid underexposure and overexposure. Coating and Drying Even with the best emulsions and cleanest screens, "pinholes" can still occur if the screen is not coated and dried properly. For better coating, it is relatively easier to use a matt film than a direct emulsion. When direct emulsions are used, the screens should be coated with a slot coater and applied slowly and smoothly with the thinner edges of the applicator. The resulting emulsion layer should be very smooth and even smooth. I generally recommend applying it twice on one side of the substrate and applying it twice on the squeegee side of the screen. In most cases, this ensures that the emulsion layer has a sufficient thickness but is not too thick. Recently developed direct sensitizing emulsions consisting of highly cured ingredients usually do not require repeated coating and drying to obtain a "pinhole free" screen. However, if you use a low-curing composition with a photographic emulsion or if the number of screens is less than 110 lines/inch, after the initial coating is dry, you still need to repeat the coating on the side of the film. The probability of using a matt film to create a "pinhole" is very small, because the screen has been fully cleaned and is in a dust-free state. Moreover, defects in the coating can be noticed immediately and you can remove the glossy film, clean the screen and use a new one. Remember to match the thickness of the matte film used to the number of lines on the screen. Thin-glossed films are used in high-mesh lines and thick-glossy films are used in low-line lines. Normally, a thin matte film and a low screen number of screens are not easily bonded. Whether it is a direct emulsion or a matte film, it needs to be dried in a dust-free and low-humidity environment. The ideal environment for drying the screen is: 80-90 degrees Fahrenheit, 40% relative humidity. Do not use heat to increase the speed of drying, and do not reduce the humidity to speed up the drying process. The humidity of the control screen drying space is a key factor in controlling the "pinhole". High humidity causes a phenomenon in which the emulsion coating looks dry and actually contains too much moisture. When these screens with humidity are exposed and rinsed, tiny fine "pinhole" images appear as a result. This screen shows underexposure, but it is not underexposure but the result of the large amount of moisture remaining in the emulsion before exposure. (This is why the screen version of the entire winter was well-made, but in the month of July there was a "pinhole".) The only solution was to dry the screen in a humidity-controlled environment. Just as I said before, do not dry on the floor, do not dry in front of the fan. The floor is the dirtiest part of the workshop. The wind blown by the fan will have a lot of fine dust. The fine dust that falls on the screen will form a “pinholeâ€. Exposure process In addition to dirty screens, the two most likely causes of “pinholes†are the lens of the exposure unit is dirty and the screen plate is underexposed. You must clean the lens before exposure, without inks, emulsions, adhesive or sticky residue, red film, or other light-blocking substances. It is best to prepare an industrial lens cleaning nozzle, a non-off-line wipe, and a window cleaning rubber for standard cleaning before exposure. If the exposure unit is flipped, clean the side that is not in contact with the screen for at least one week. Underexposure is another common cause of pinholes. Of course, some screen printers carefully control the underexposed screen for details, but other underexposures are due to the lack of proper calibration of the screen exposure process. The underexposure features are as follows: The emulsion film is thin after development; 2. There is a row of "pinholes" on the edge of the original image. The image is incomplete during the printing process; 4. The screen is not easy to reproduce. The only way to correct underexposed screens is to use an exposure calibrator to calibrate the screen exposure process. All emulsion manufacturers sell exposure calibrators, which generally correspond to the emulsion used. For those who are underexposed to get fine details, a different emulsion, a screen-high number of dye meshes, a matte film, a positive sheet instead of a sulfated paper is used as the exposure manuscript, and a better light source is used. Image development Contrary to what many printers imagine, the development process is not the cause of “pinholesâ€. The reason why “pinholes†are generated after rinsing is usually underexposure or dust particles are in the emulsion. The screens that are properly prepared and exposed are very durable and generally resistant to the 1000psi pressure stream. Screens that have been carefully made during the printing operation may also appear as "pinholes" during the printing process. In most cases, the “pinhole†in the printing is caused by the dust particles contained in the emulsion. After the emulsion layer is worn out during the printing process, a small hole or a bubble is left (the cause of the air bubbles is mainly coated. Shortly or after coating, there is not enough time for the bubbles to run out of the photoreceptor layer). If the "pinhole" appears parallel to the squeegee, check that the "pinhole" is in the same area before and after the squeegee. The pressure of the squeegee to the screen is greatest at both ends, so if the "pinhole" occurs where the squeegee passes, it may be that the squeegee exerts excessive tension or even damage to the emulsion layer. They excessively pull the screen so that the emulsion layer breaks or falls off. If this is the case, the method of reducing the distance to contact, using a shorter squeegee, making the squeegee corners more rounded, and using a large screen version can be used. Personnel training A well-trained, quality-conscious screen maker can also produce “pinhole-free†screens under the most difficult conditions, even when the work is very difficult and screen quality is inconsistent. Satisfactory product. On the contrary, poorly trained savage screen makers may produce inferior products even with the best screening equipment. Most emulsion manufacturers provide complete, accurate, and detailed instructions and charts for each product. In fact, this information is not new information that has just come out, but it is commonly used information. I hope that you have mastered them. Use this article as a training guide to create a "pinhole" screen-free operating procedure. For example: 1. Clean the screen thoroughly; 2. Clean the exposure unit lens before each exposure; 3. Properly expose the screen. If you can follow the instructions in each section of this article, it should be an easy task to create a "pinhole-free" screen. I hope this article can bring you profits and bring benefits.
Ottomans Furniture
Ottomans Furniture
Ottomans with rattan hand weaving style and aluminium powder-coated frame, you can sit or put your foot on that and rest yourself competely. Ottomans together with the lounge chair generally, you can relax and enjoy your life.
Even some ottoman have storage function, you can put pillow, books or small items on that.
Handwoven premium resin wicker UV resistant
Rust-resistant powder-coated frames
Cushions included with 30 density sofa foam
Versatile tempered glass tables
Cushions also available with 100% waterproof fabric.
Outdoor ottomans furniture with different style and hand weaving
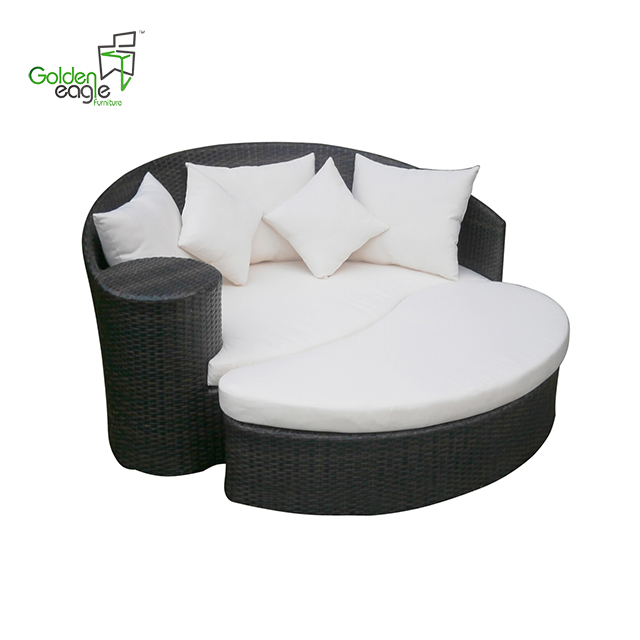
If you have any questions, please contact with us directly. Outdoor Sofa Furniture are produced
by Golden Eagle Outdoor Furniture With High Quality and Good Appearance. Welcome you can visit our Factory.For any inquiry,Please send mail directly to us.
Ottomans Furniture,Wicker Ottomans Furniture,Ottoman Leather Furniture,Modern Ottomans Furniture
Golden Eagle Outdoor Furniture Co., LTD. , https://www.gegardensets.com